We’ve already covered what NDT stands for and how the phrase is used in the field. Now let’s dive in and look more closely at some of the details that govern the world of NDT.
DESTRUCTIVE VS. NON-DESTRUCTIVE TESTING
Before we go any further, we should clarify that there are some methods used to test materials that alter—or even damage and destroy—the materials tested.
The use of these methods is called Destructive Testing.
In Destructive Testing, a piece of the material might be scraped away for analysis or altered in some way onsite.
Here are some examples:
- Macro sectioning. Macro sectioning tests a small section of a welded material by polishing and etching it for examination.
- Tensile testing. Also called tension testing, this is a destructive testing technique that uses controlled tension applied to a sample material to see how it reacts. Tension could be applied to test certain loads or conditions, or to test a material’s failure point.
- 3 point bend testing. 3 point bend testing examines the soundness and flexibility (or ductility) of a material by taking a sample of it, called a coupon, and bending it in three points to a specified angle.
NDT CODES AND STANDARDS
NDT techniques can be used for all kinds of inspections. But some of the most important types of NDT inspections are of assets like boilers and pressure vessels, which could be incredibly dangerous if not properly maintained.
Because proper maintenance of these assets is so important for the safety of those working nearby (or even at a distance, when it comes to nuclear power plants), most countries have laws requiring companies to adhere to specific inspection codes and standards when conducting inspections.
These standards and codes typically require inspections to be conducted periodically following specific guidelines. For the most assets that present the greatest risk, these inspections must be both conducted by a certified inspector and approved by a certified witness working for a formal inspection body.
Here are the most commonly followed organizations in the world for creating NDT standards and codes:
- API (American Petroleum Institute)
- ASME (American Society for Mechanical Engineers)
- ASTM (American Society for Testing and Materials)
- ASNT (American Society For Nondestructive Testing)
- COFREND (French Committee for Non-destructive Testing Studies)
- CSA Group (Canadian Standards Association)
- CGSB (Canadian General Standards Board)
WHY USE NDT?
Here are the top reasons NDT is used by so many companies throughout the world:
- Savings. The most obvious answer to this question is that NDT is more appealing than destructive testing because it allows the material or object being examined to survive the examination unharmed, thus saving money and resources.
- Safety. NDT is also appealing because almost all NDT techniques (except radiographic testing) are harmless to people.
- Efficiency. NDT methods allow for the thorough and relatively quick evaluation of assets, which can be crucial for ensuring continued safety and performance on a job site.
- Accuracy. NDT methods have been proven accurate and predictable, both qualities you want when it comes to maintenance procedures meant to ensure the safety of personnel and the longevity of equipment.
“Nondestructive testing is the life blood of a well-run facility. NDT techniques and repeatable results depend on highly trained technicians with experience and integrity. Industrial NDT methods and interpretation of results are performed by certified professionals. Not only does the technician need to be certified in a specific NDT method, but they also need to know how to operate the equipment being used to gather data. Understanding equipment capabilities and limitations is the difference between making an accept or reject determination.”
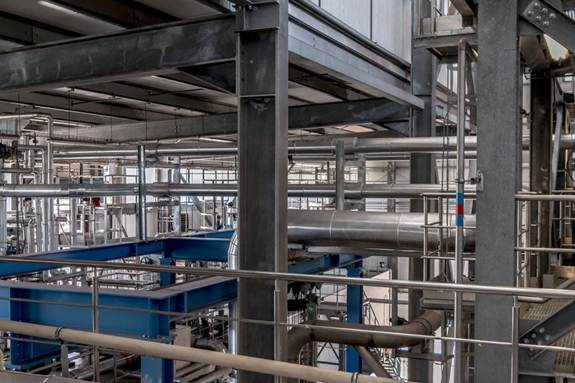